Forklifts serve as the backbone of numerous industries, relentlessly transporting goods across warehouses, construction sites, and manufacturing facilities.
However, when operated in harsh environments, these vehicles face conditions that can significantly accelerate wear and tear. Extreme temperatures, corrosive materials, dust, and moisture can all take their toll, affecting safety, efficiency, and the lifespan of forklifts.
Below, we’ll delve into essential maintenance tips to ensure your forklifts remain reliable and safe, even in the most challenging conditions.
Harsh Environmental Conditions
Harsh environments for forklifts include areas with extreme temperatures, high humidity, corrosive chemicals, and significant dust or debris. These conditions can lead to increased mechanical wear, electrical system failures, and corrosion. Recognizing the signs of wear and understanding the impact of these environments on your equipment is the first step in effective maintenance.
8 Harsh Environment Forklift Maintenance Tips
These maintenance tips will help to prevent forklift breakdown in harsh environmental conditions, keeping you operating at full capacity.
Tip #1: Do a Pre-Operation Inspection
Before operating a forklift in harsh conditions, conduct a thorough pre-operation inspection.
Check the tires for cuts or excessive wear, ensure forks are straight and free of cracks, verify that brakes respond promptly, and inspect hydraulic systems for leaks or damage. This proactive approach can prevent accidents and costly repairs.
Tip #2: Follow a Regular Maintenance Schedule
Forklifts used in harsh environments may require more frequent maintenance than those used under normal conditions. Consult the manufacturer’s maintenance schedule as a starting point, but adjust it based on real-world experiences to create a forklift maintenance checklist that suits your needs. Pay special attention to parts most affected by your specific environment, such as filters in dusty conditions or hydraulic systems in cold climates.
Tip #3: Regularly Clean and Lubricate
Regular cleaning helps prevent the buildup of materials that can damage your forklift. Use appropriate cleaning methods for your environment, such as pressure washing for mud or dust, and neutralizing agents for corrosive substances. Follow up with proper lubrication to protect moving parts from wear and corrosion.
Tip #4: Care for Your Battery and Electrical System
In extreme conditions, battery and electrical systems require extra care. Perform regular forklift battery maintenance checks. Keep battery terminals clean and check for corrosion, ensuring that all connections are secure. Protect electrical components from moisture and dust, which can lead to short circuits or other failures.
Tip #5: Inspect Tires and Undercarriage
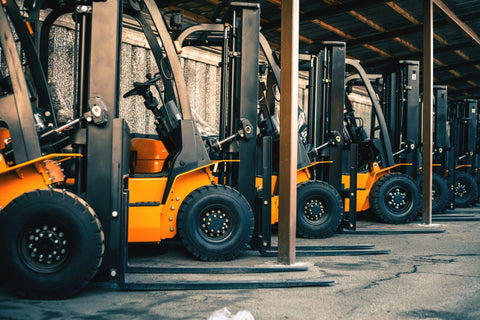
Tires must be inspected regularly for signs of damage, such as cuts or embedded objects, especially when operating on rough terrain. The undercarriage should also be checked for debris that could hinder movement or damage components. Regular inspections and maintenance will help avoid unexpected downtime.
Tip #6: Oversee Training and Awareness
Operators should be trained not only on how to use forklifts but also on how to maintain them under harsh conditions. A well-informed team can recognize early signs of wear and tear, preventing minor issues from becoming major problems. Foster a maintenance-minded culture among your workforce to keep your equipment and operators safe.
Tip #7: Leverage Technology
Modern technologies, such as diagnostic software and fleet management systems, can be invaluable in monitoring the health of your forklifts. These tools can provide real-time data on vehicle performance, predict maintenance needs, and help manage the maintenance schedule more effectively.
Tip #8: Prioritize Safety Features and Ergonomics
Never overlook the forklift’s safety features. Ensure that lights, horns, and backup alarms are fully functional. Consider the ergonomics of operating a forklift in harsh conditions and make adjustments to reduce operator fatigue, such as installing more comfortable seating or climate controls in cabins.
Invest in Quality Seats for Operator Comfort and Safety
Maintaining your forklifts in top condition in harsh environments is not just about mechanical and electrical care; it also extends to ensuring operator comfort and safety through high-quality seating.
Seats exposed to extreme conditions can degrade, affecting operator comfort and productivity.
We encourage you to assess your forklift seats regularly and consider replacing any that show signs of wear or damage due to harsh conditions.
Explore our selection of Toyota forklift seats and other replacement forklift seat options designed to enhance operator comfort and safety.
Investing in quality seating is a step toward maintaining not only the efficiency of your operations but also prioritizing the well-being of your operators. Shop with us today and ensure your forklifts are equipped to meet the challenges of any environment, while providing the best support for your team.